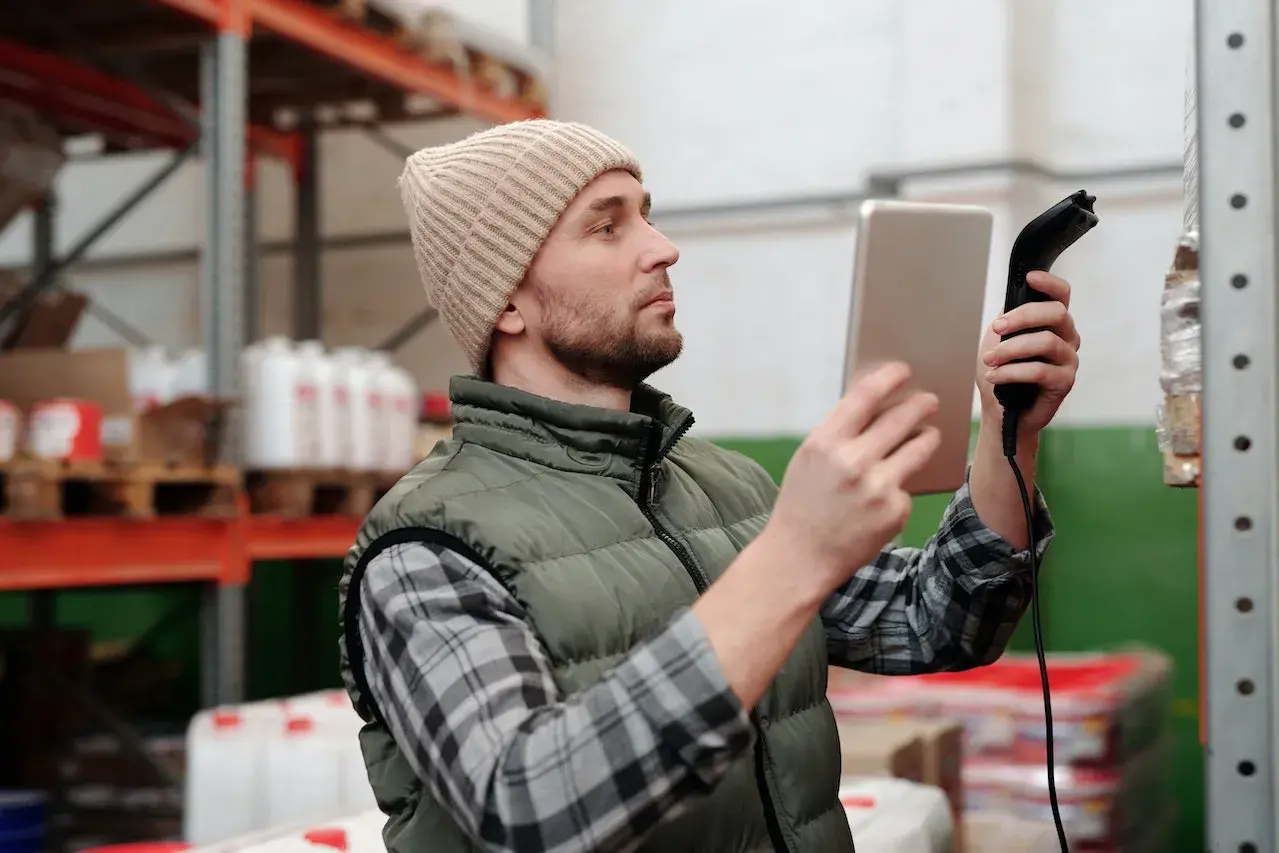
Inventory & Stock Reconciliation – Importance, Examples, Challenges & Best Practices
Inventory reconciliation or stock reconciliation is the process of comparing and verifying the accuracy of a company’s physical inventory with the inventory records in its accounting system. The purpose of this process is to ensure that the company’s financial records accurately reflect the actual physical inventory it has on hand, and to identify and correct […]
Read More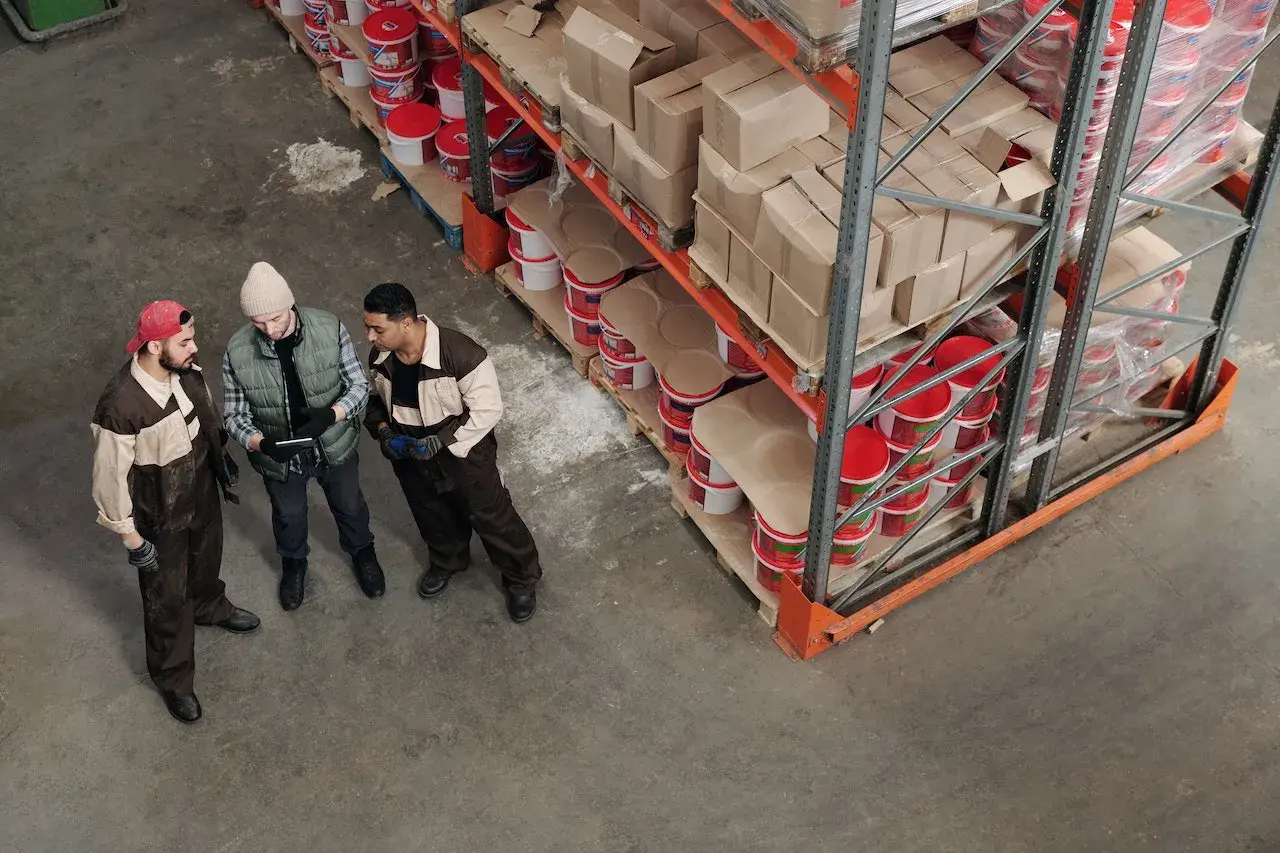
Warehouse Management – Definition, Operations & Best Practices
Warehouse management refers to the processes and systems used to control and coordinate the storage, handling, and distribution of goods within a warehouse. The goal of warehouse management is to ensure that the right products are stored in the right place at the right time, and that they are readily available for order fulfillment, while […]
Read More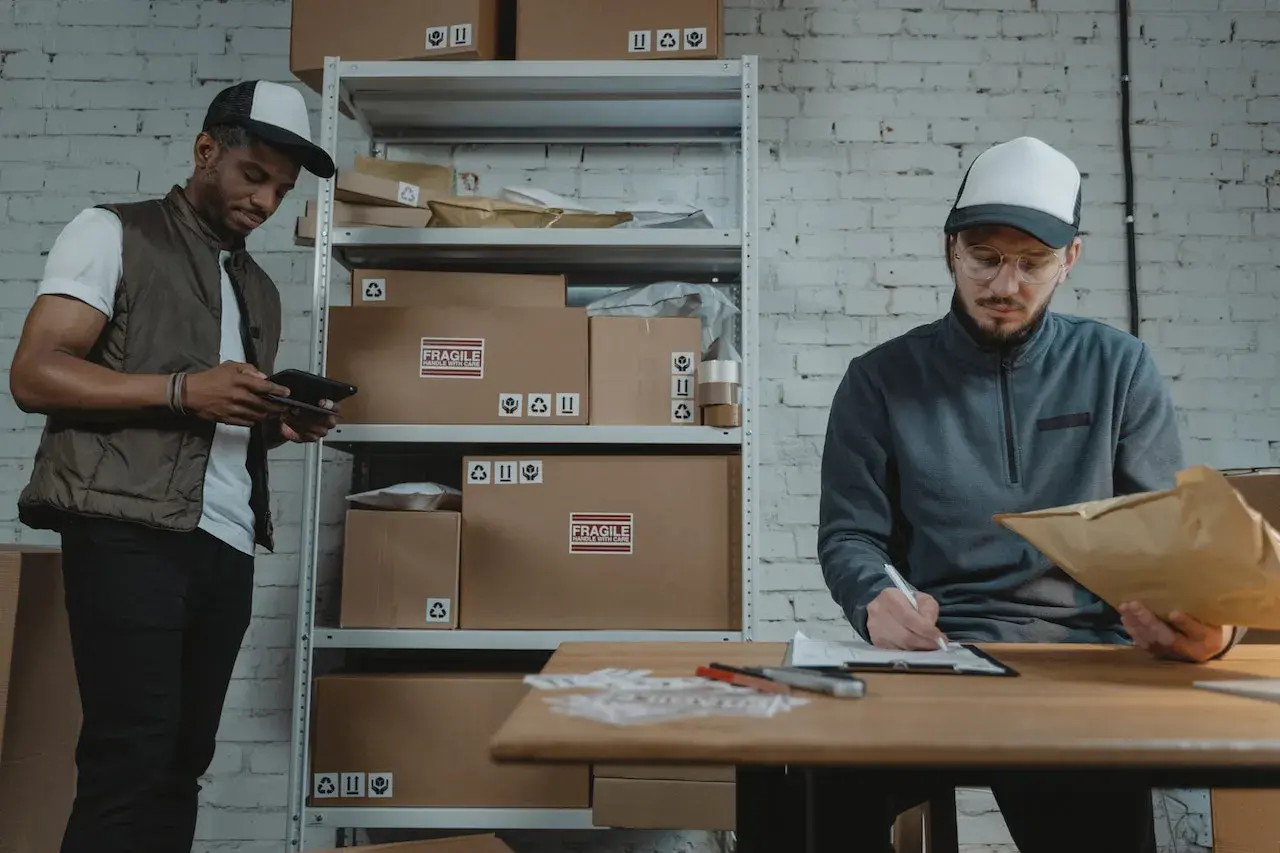
Conquer Inventory Accuracy: 12 Cycle Counting Methods & Best Practices
An inventory cycle count is a process of regularly verifying the physical quantity of a subset of your inventory items against the recorded amounts in your inventory management system. It’s essentially a mini-inventory audit that’s conducted on a continuous, planned basis, instead of just once a year like a traditional full inventory count. Here’s how […]
Read More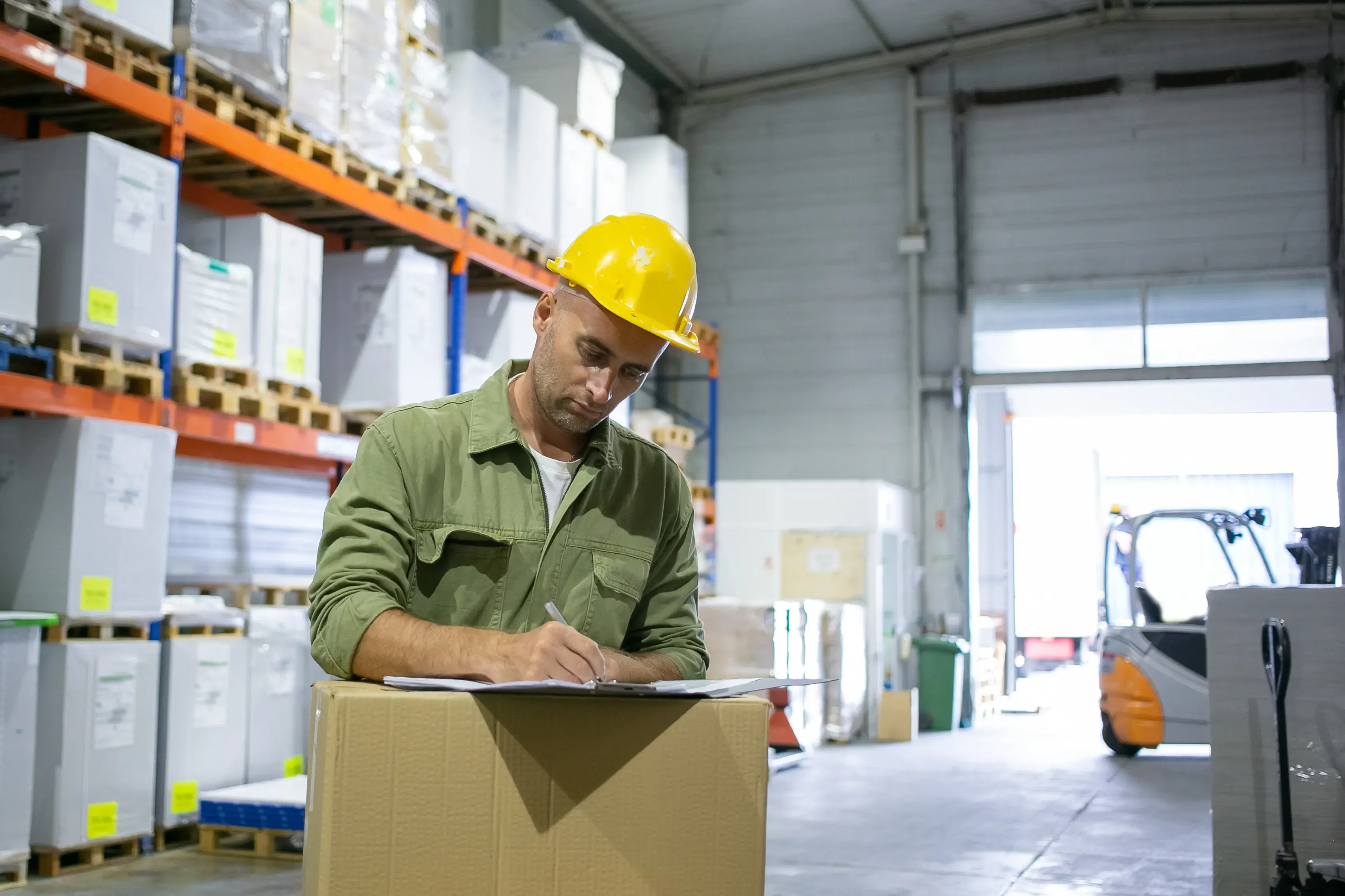
Inventory Audits: 9 Essential Procedures for Accuracy, Efficiency, and Compliance
An inventory audit is a systematic process of cross-checking a business’s financial records with its physical inventory and records. This process helps ensure that the company’s inventory levels are accurate and consistent with its financial statements. Inventory audits are critical for businesses that deal with physical products, as they provide essential insights into inventory management […]
Read More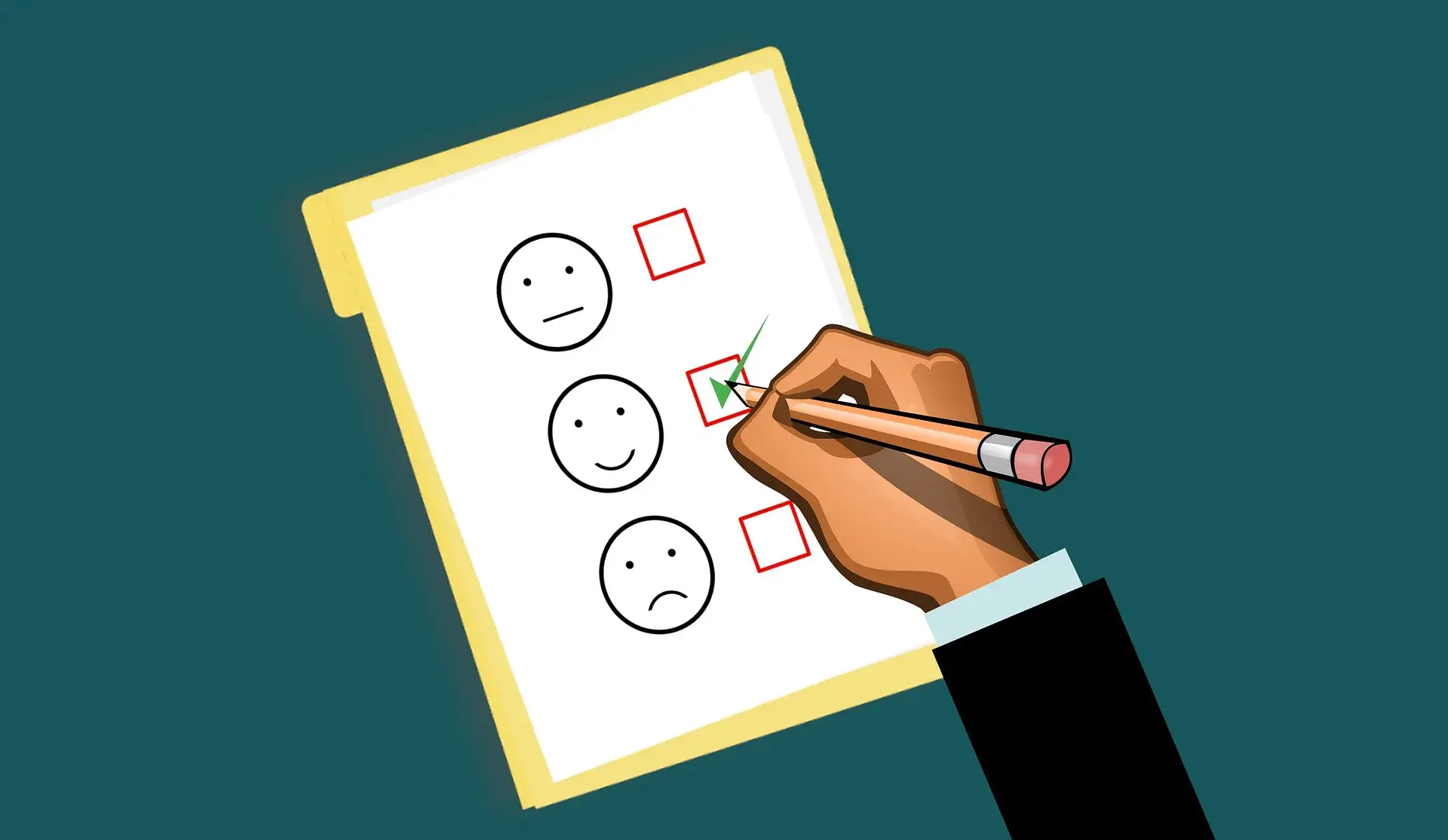
The Impact of Inventory Management on Customer Satisfaction
Inventory management refers to the process of monitoring and controlling a company’s inventory levels, including the raw materials, work-in-progress, and finished goods. It involves tracking inventory levels, determining the optimal inventory levels, and managing the ordering and storage of inventory to meet customer demands. Effective inventory management is significant for businesses because it ensures that […]
Read More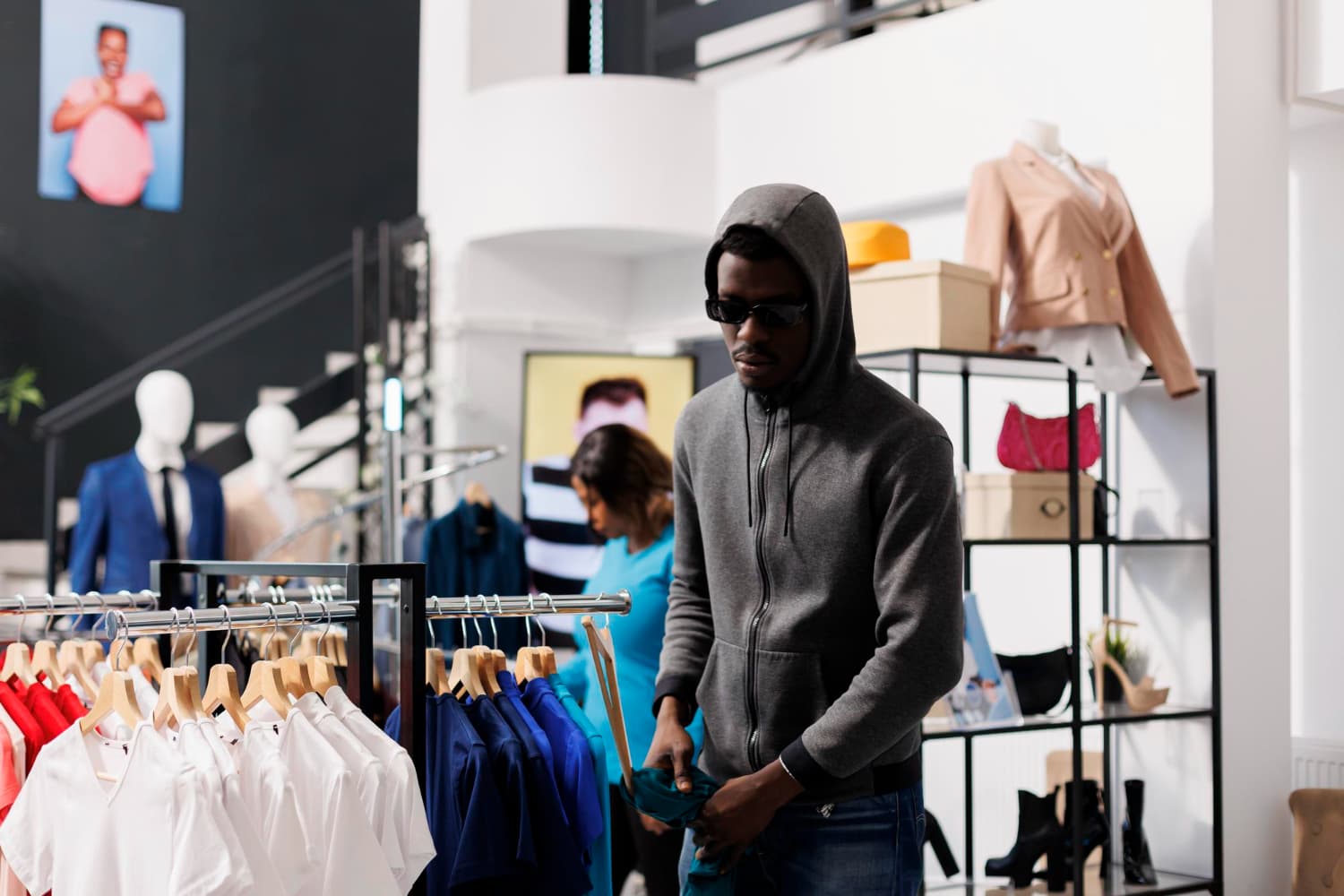
Inventory Shrinkage: Understanding, Managing, and Preventing Loss in Your Business
Inventory shrinkage occurs when the physical count of inventory is less than what is recorded in the accounting system. This discrepancy can be due to various factors, including theft, damage, errors in record-keeping, or supplier fraud. According to NRF’s Retail Security Survey 2022, “Retail shrink is an almost $100 billion problem.“ Inventory shrinkage is a […]
Read More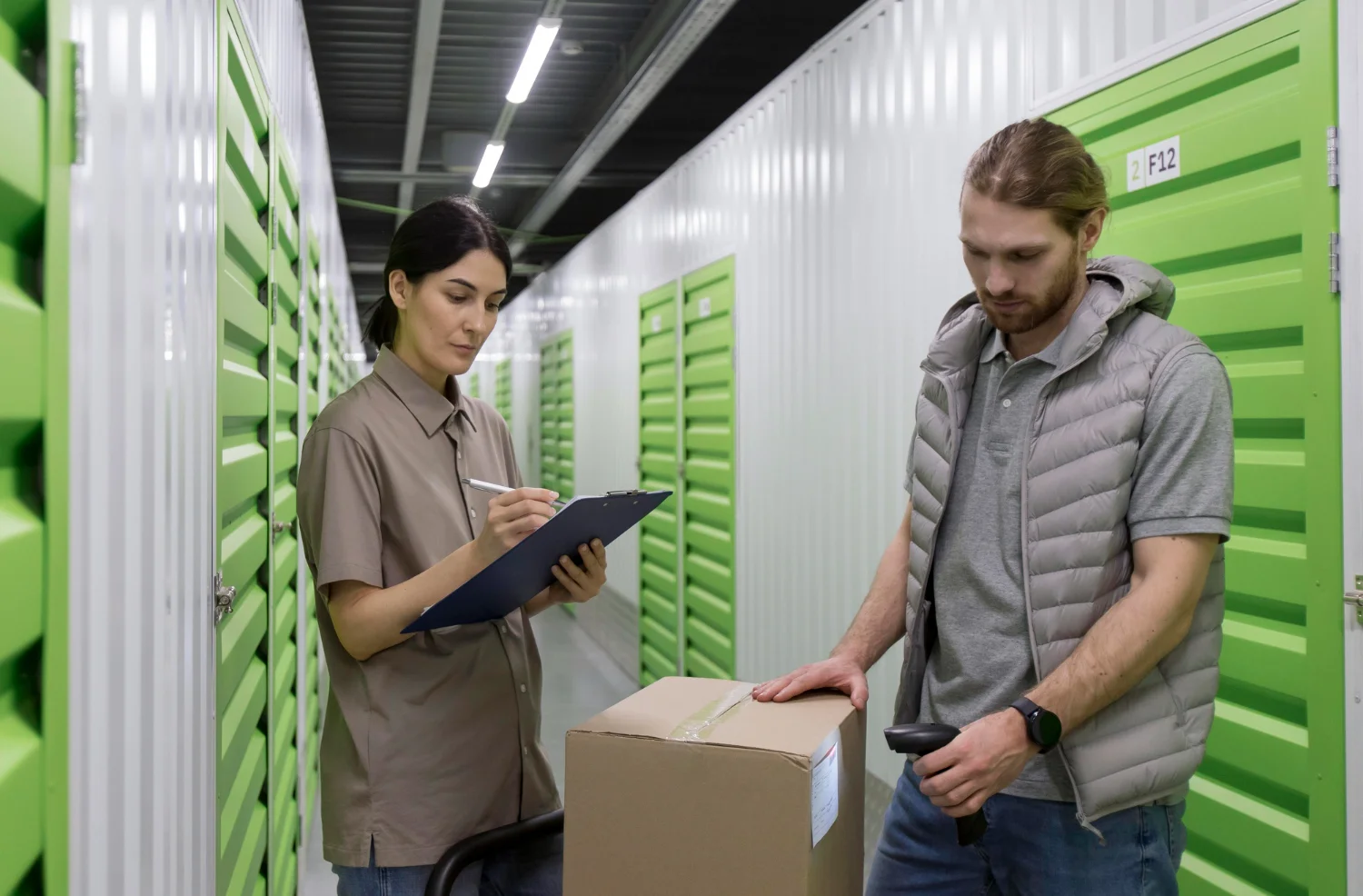
Lot Tracking: Effective Supply Chain Management
Lot tracking is a process of tracing the movement of a specific batch or lot of products or materials throughout the supply chain. It involves assigning a unique identification code to each lot of items and recording its details, such as production date, expiration date, and location. In today’s fast-paced, highly regulated world of manufacturing and […]
Read More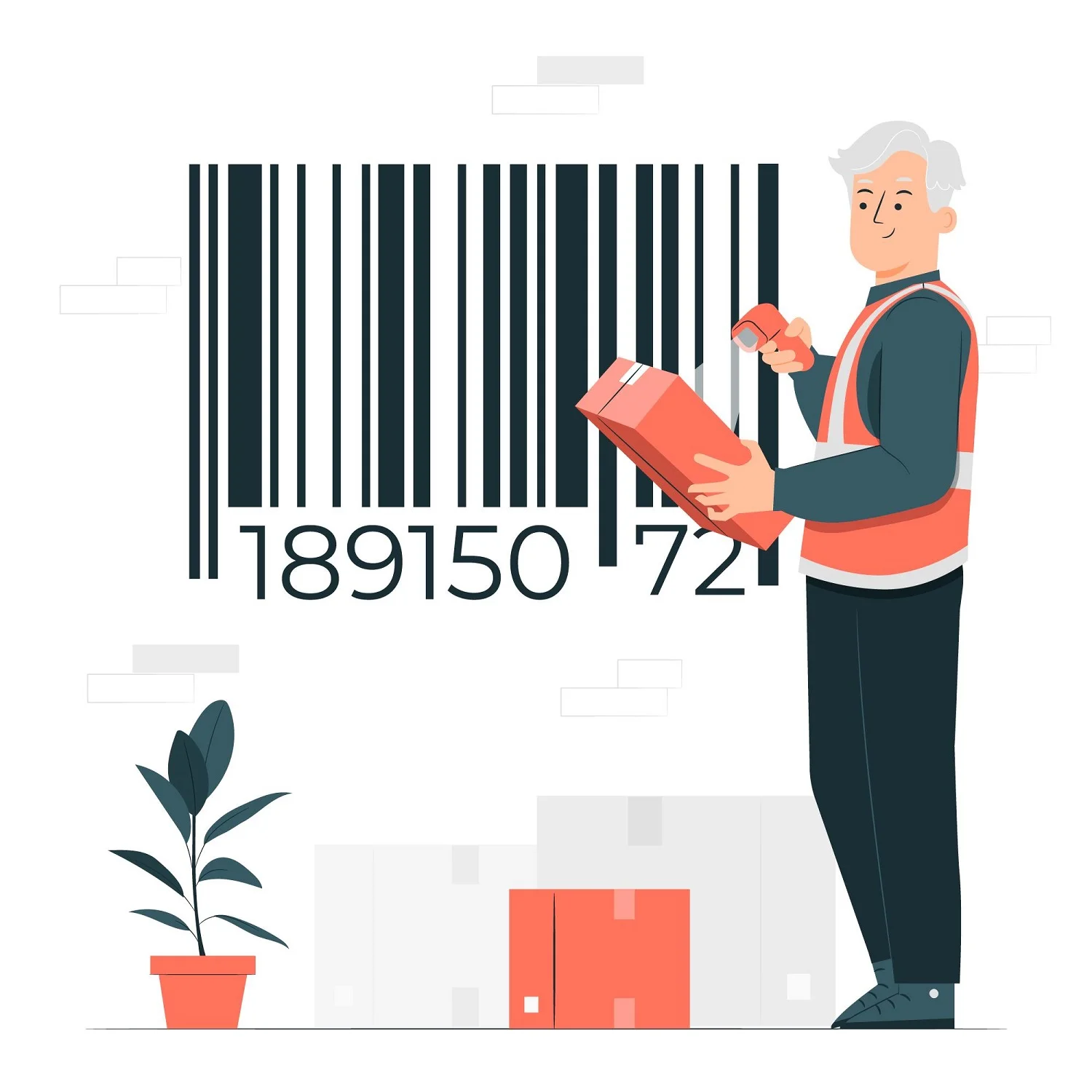
Serial Number Tracking: A Comprehensive Guide for Small Business Owners
Serial number tracking is the practice of assigning and tracking a unique serial number to individual products or components throughout their entire lifecycle. This involves using a specific identification code to track and monitor products as they move through various stages of production, distribution, and sale until they reach the end customer. The primary purpose […]
Read More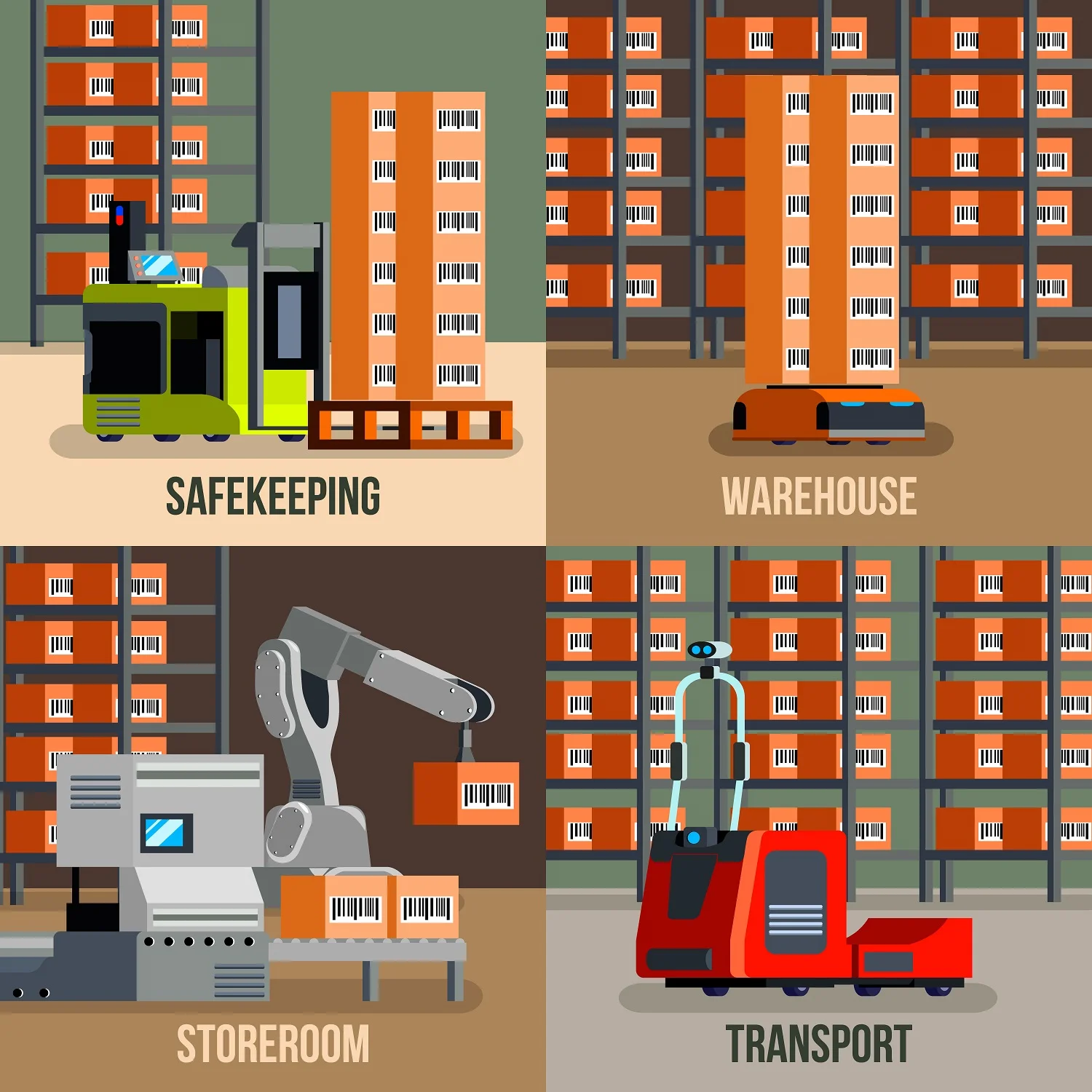
Multiple Units of Measure in Inventory Management
Multiple units of measure refer to the practice of measuring and tracking inventory using different units of measure, such as weight, volume, length, or quantity. For example, a business might purchase raw materials in pounds, store them in inventory by volume, and sell them by the unit. Managing inventory with multiple units of measure can […]
Read More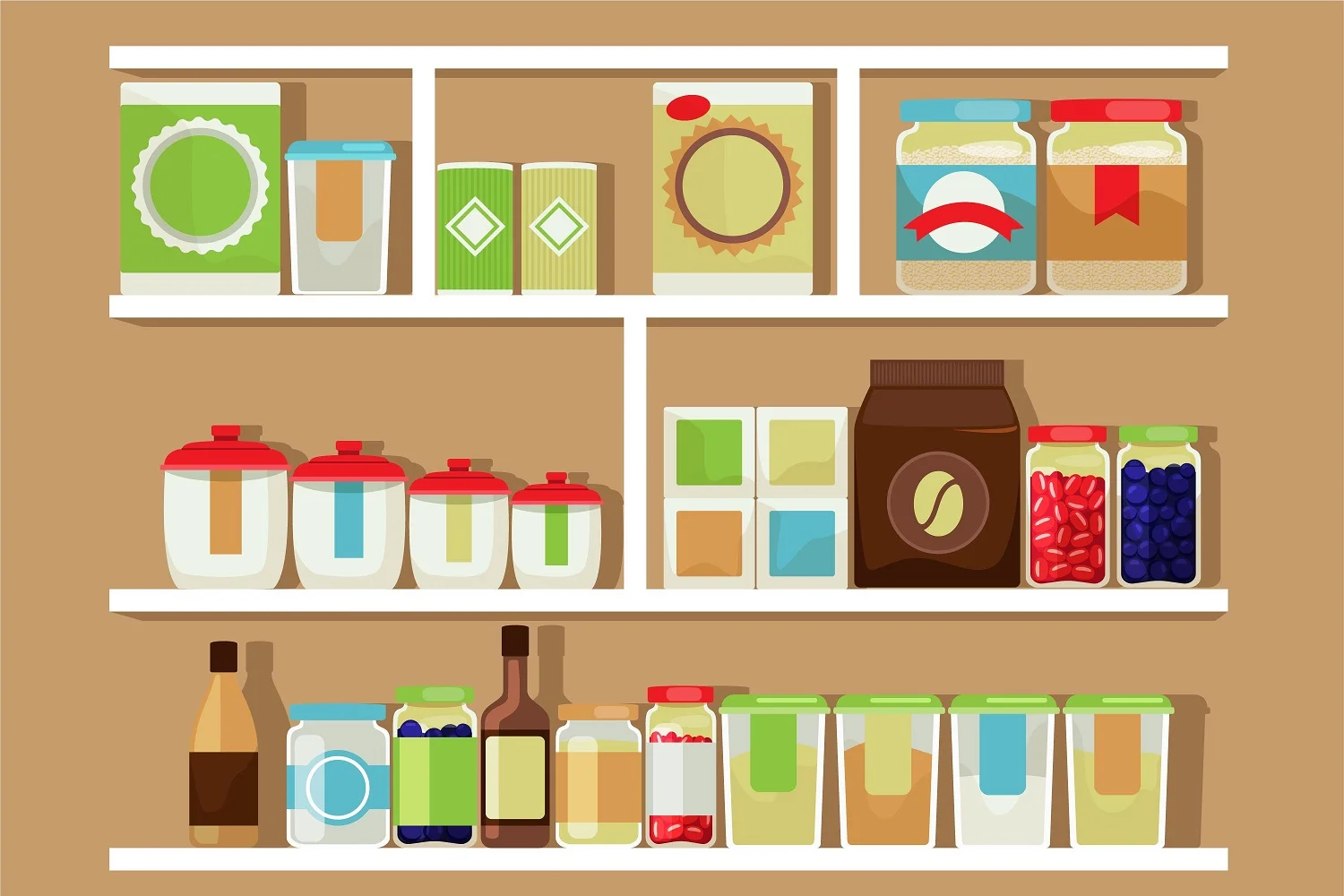
Item Groups 101: How to Organize Products with Multiple Variants
When selling a product with multiple variants, such as different sizes or colors, it’s important to group them together so that customers can easily select the one they want. One way to do this is by creating an “item group” that includes all the variants of the same product. An item group is a collection […]
Read More