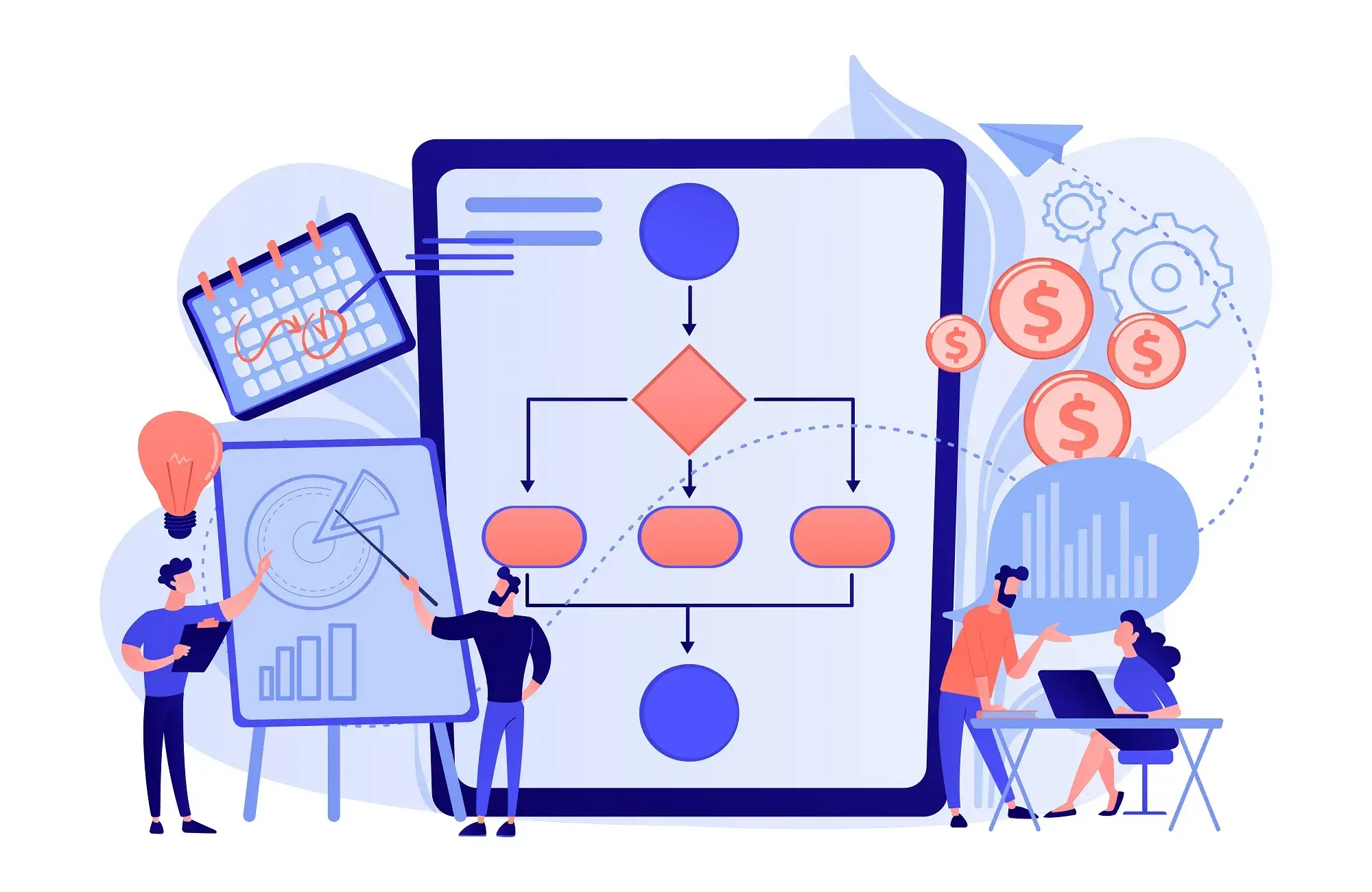
How Inventory Management Impacts Your Company’s Financial Performance
Inventory management refers to the process of overseeing, organizing, and controlling a company’s inventory levels to ensure that the right products are available in the right quantity at the right time. It involves managing the flow of goods from the manufacturer or supplier to the warehouse or storage facility, and then to the point of […]
Read More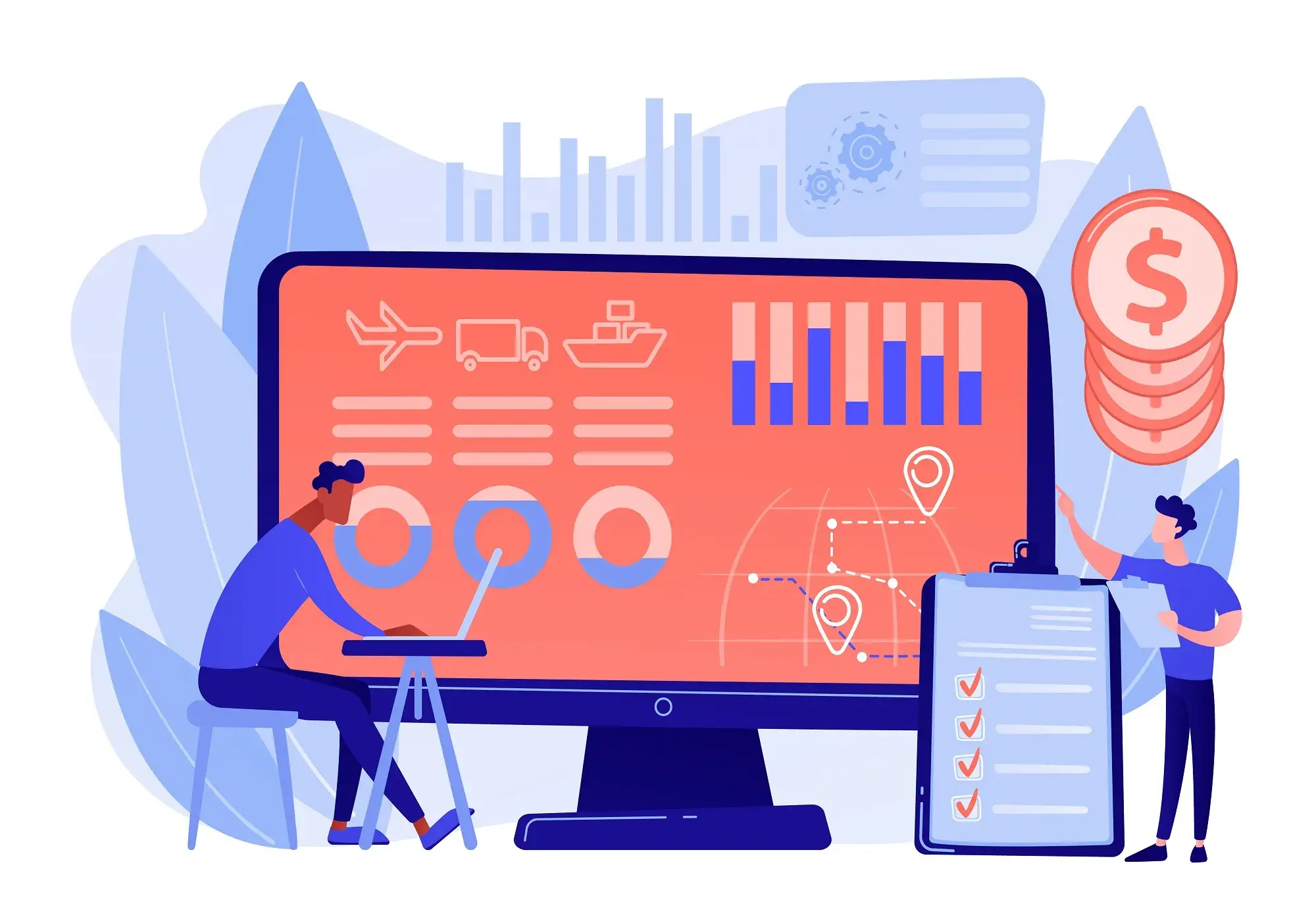
Reverse Logistics and Inventory Management: Benefits and Challenges
Reverse logistics and inventory management are two important concepts in the field of supply chain management. Reverse logistics refers to the process of managing the flow of goods from the end consumer back to the manufacturer or distributor for various reasons, such as product recalls, returns, repairs, or recycling. It involves the collection, transportation, sorting, […]
Read More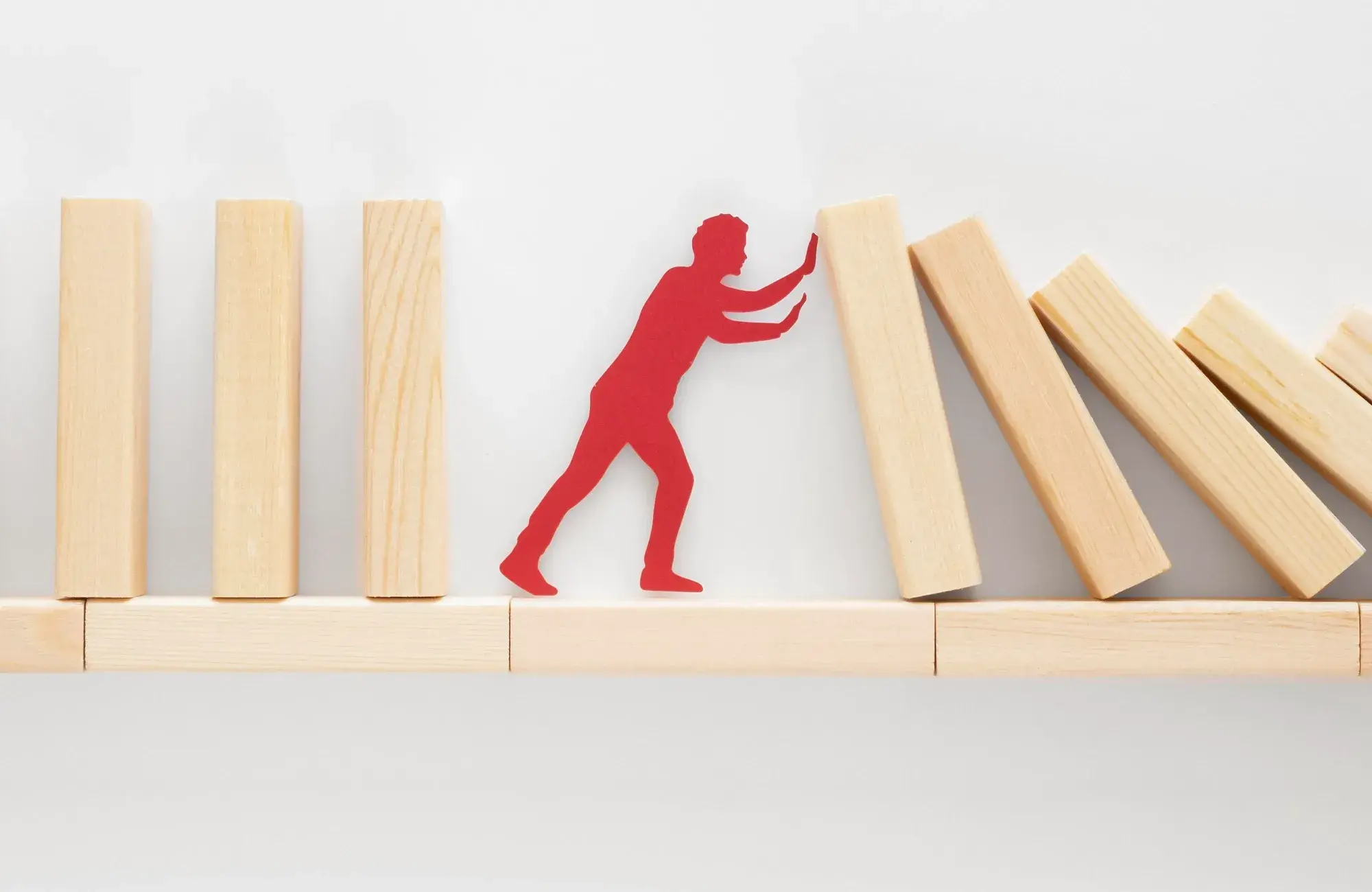
Identifying and Mitigating Inventory Risks in Your Business
Inventory risk management is the process of identifying, assessing, and mitigating the potential risks to your inventory. By effectively managing your inventory risks, you can protect your business from financial losses, maintain customer satisfaction, protect your reputation, and maintain efficient operations. Effective inventory risk management includes assessing potential risks, implementing risk mitigation strategies, and continuously […]
Read More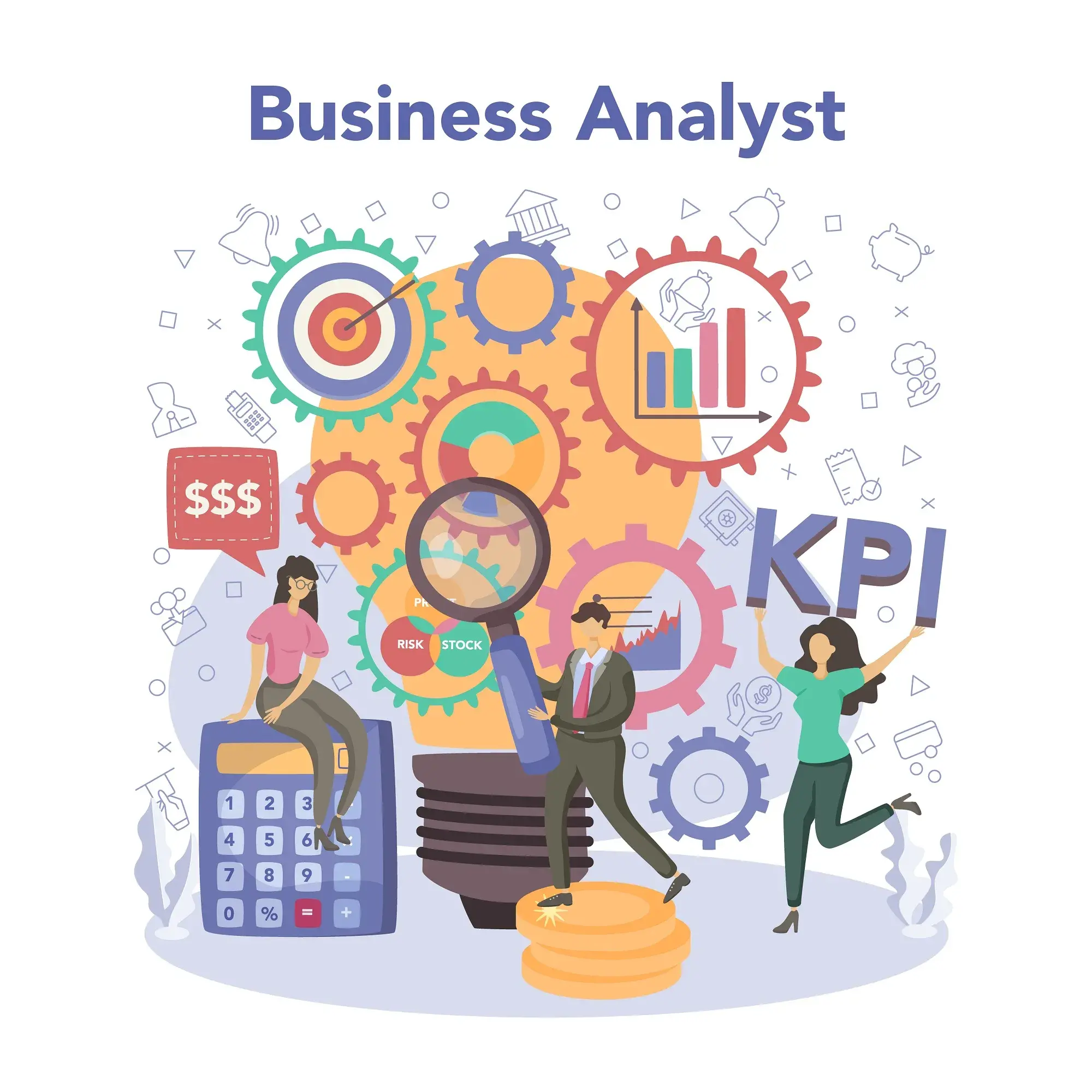
Measuring Inventory Performance: 20 Metrics and KPIs That Matter
Inventory metrics and KPIs are measurements that help you track and assess the performance of your inventory management. They can be used to identify areas where your inventory management is working well, and areas where it could be improved. Why Are They Important? Inventory metrics and KPIs are important because they provide insights into the […]
Read More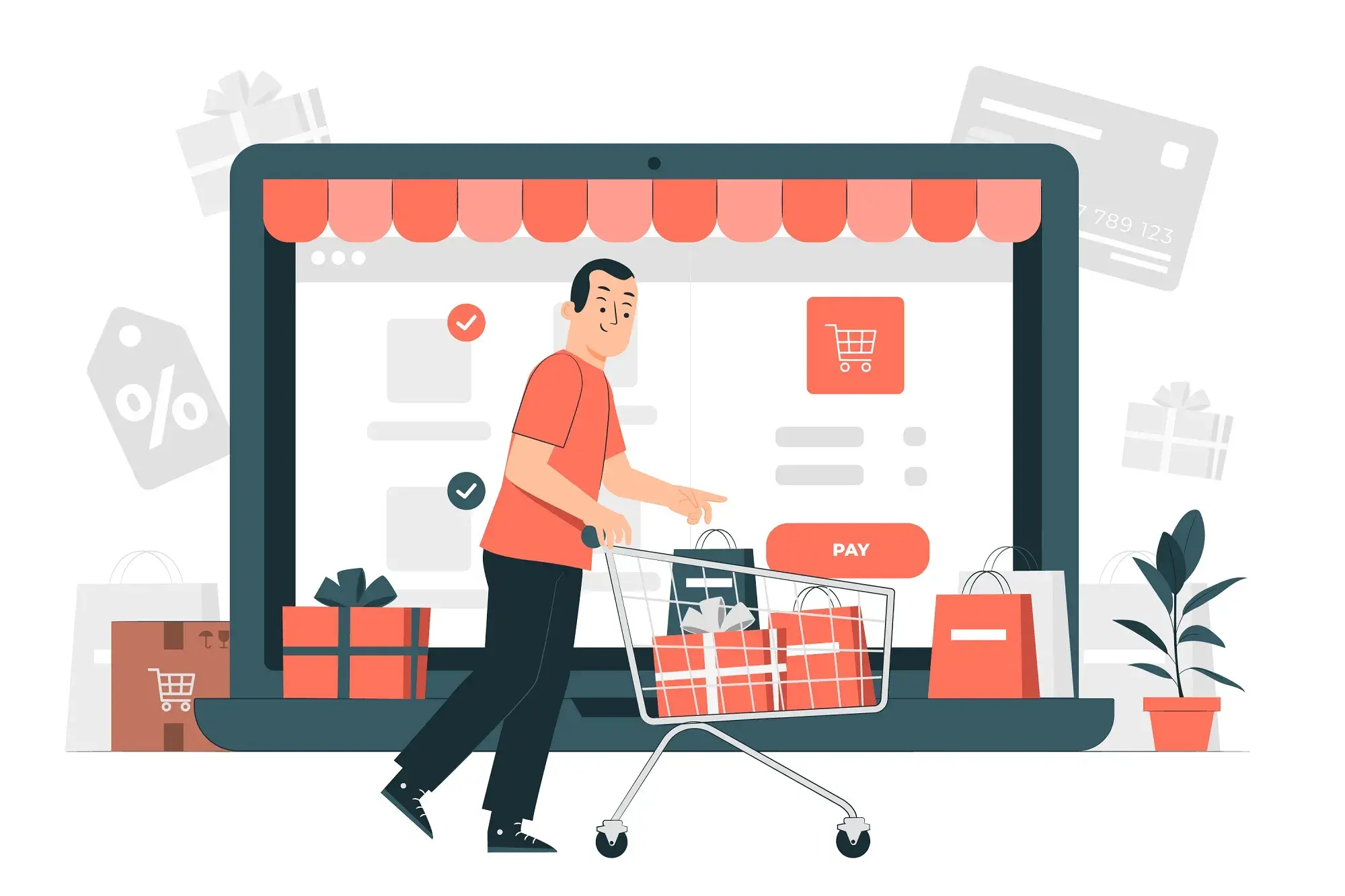
Mastering the Maze: Multichannel Inventory Management
Multi-channel inventory management refers to the process of managing and controlling inventory levels across multiple sales channels, such as online marketplaces, brick-and-mortar stores, and wholesale distributors. It involves tracking inventory levels in real-time, forecasting demand, optimizing inventory levels, and ensuring that the right products are available in the right quantities at the right locations to meet customer demand […]
Read More
Multi-Echelon Inventory Management: The Key to a Resilient Supply Chain
Multi-echelon inventory management refers to the process of managing inventory across multiple levels or tiers of a supply chain, each with its own set of inventory policies and controls. In a multi-echelon inventory system, inventory is held at multiple levels, from raw materials to finished goods, and each level may have its own suppliers and […]
Read More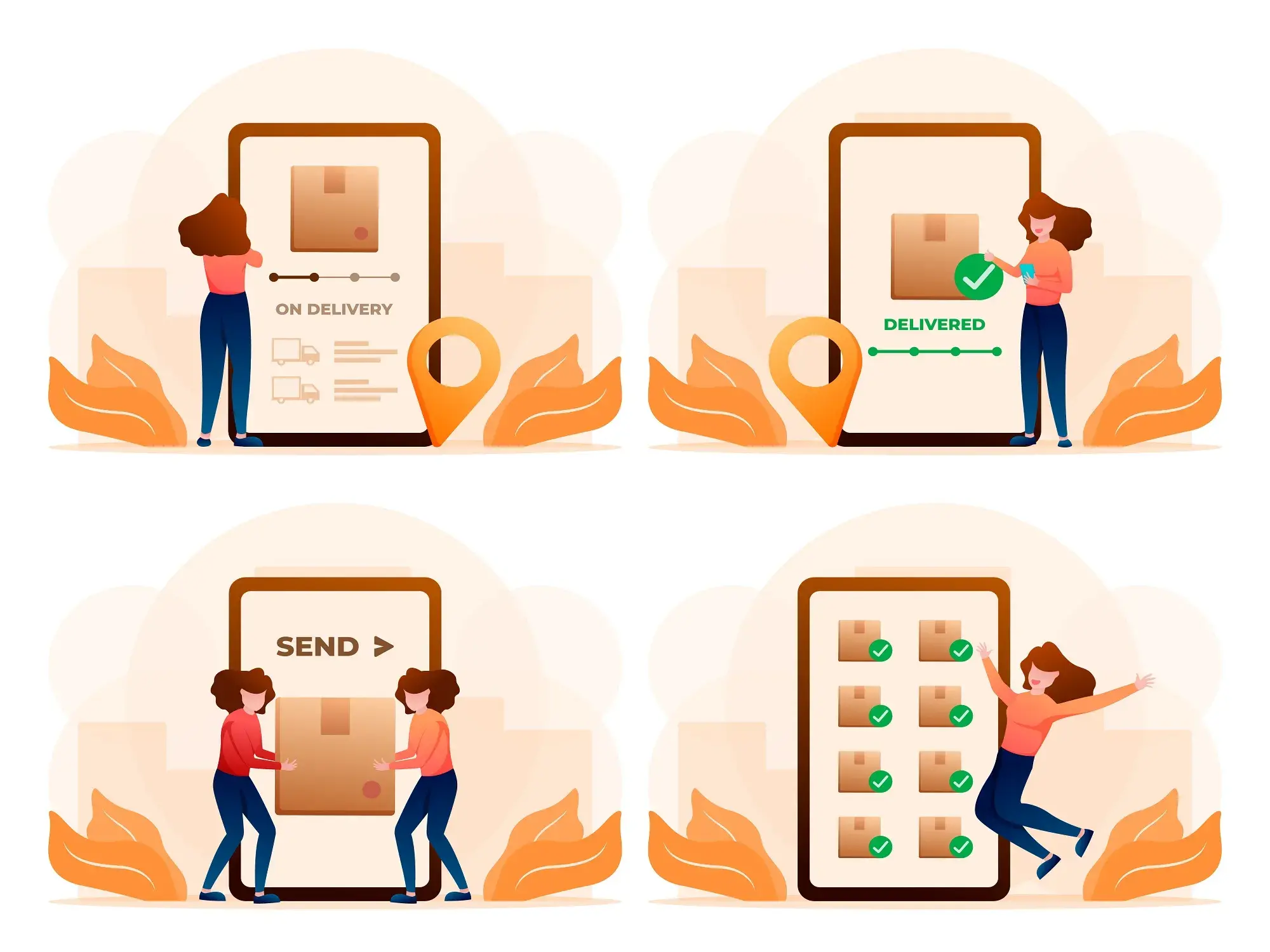
Effective Inventory Management Strategies for E-commerce Businesses
Inventory management in e-commerce refers to the processes and strategies involved in managing the flow of products or goods from the point of purchase or production to the point of sale or delivery to customers. It involves the planning, organizing, and controlling of the inventory or stock levels of an e-commerce business to ensure that […]
Read More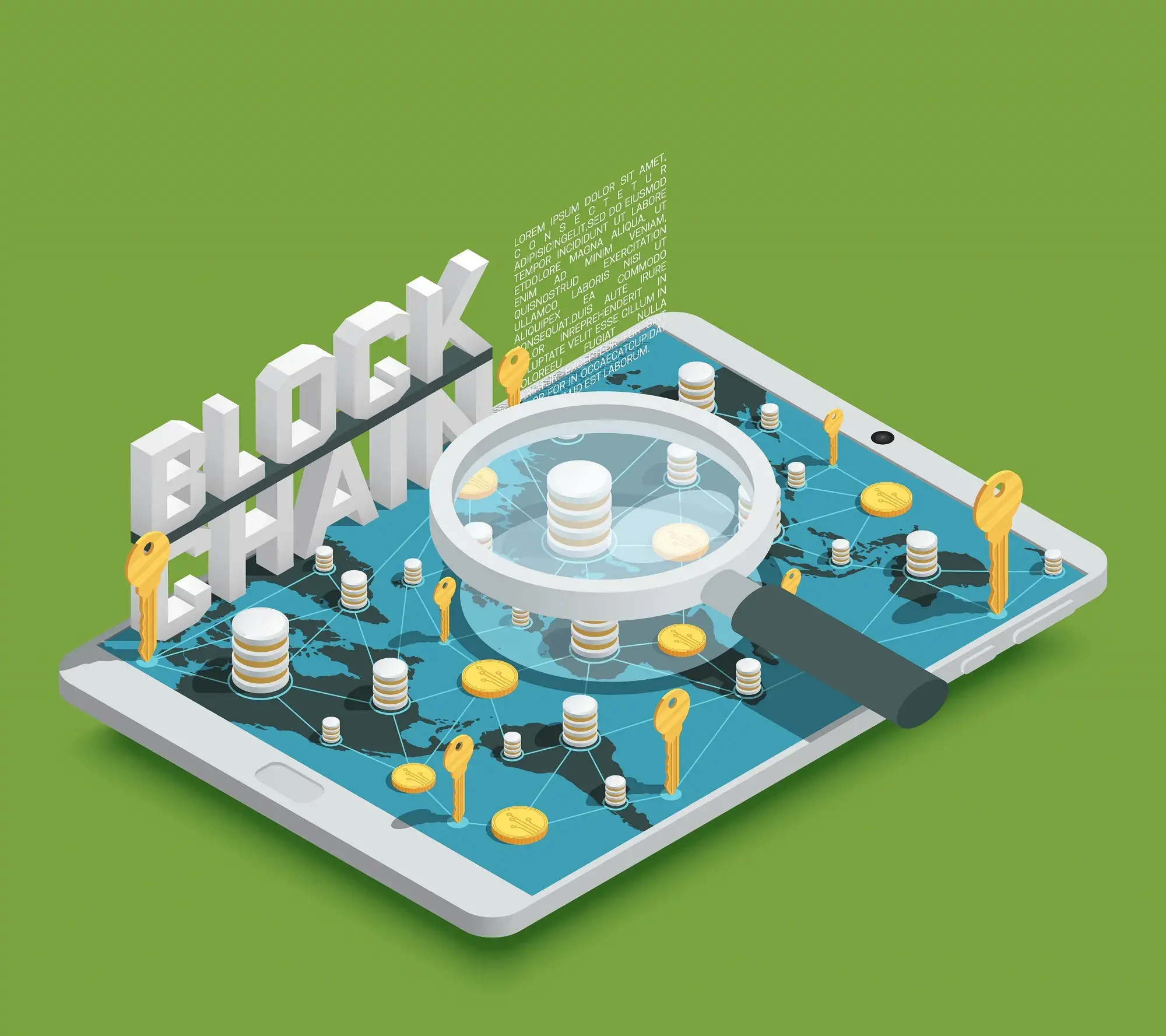
Technologies in Inventory Management: The Present & Future
Inventory management refers to the process of overseeing and controlling the flow of goods and materials in and out of a company’s inventory. It involves managing the ordering, storing, tracking, and delivery of products and materials in order to meet customer demand while minimizing costs associated with holding inventory. Effective inventory management ensures that a […]
Read More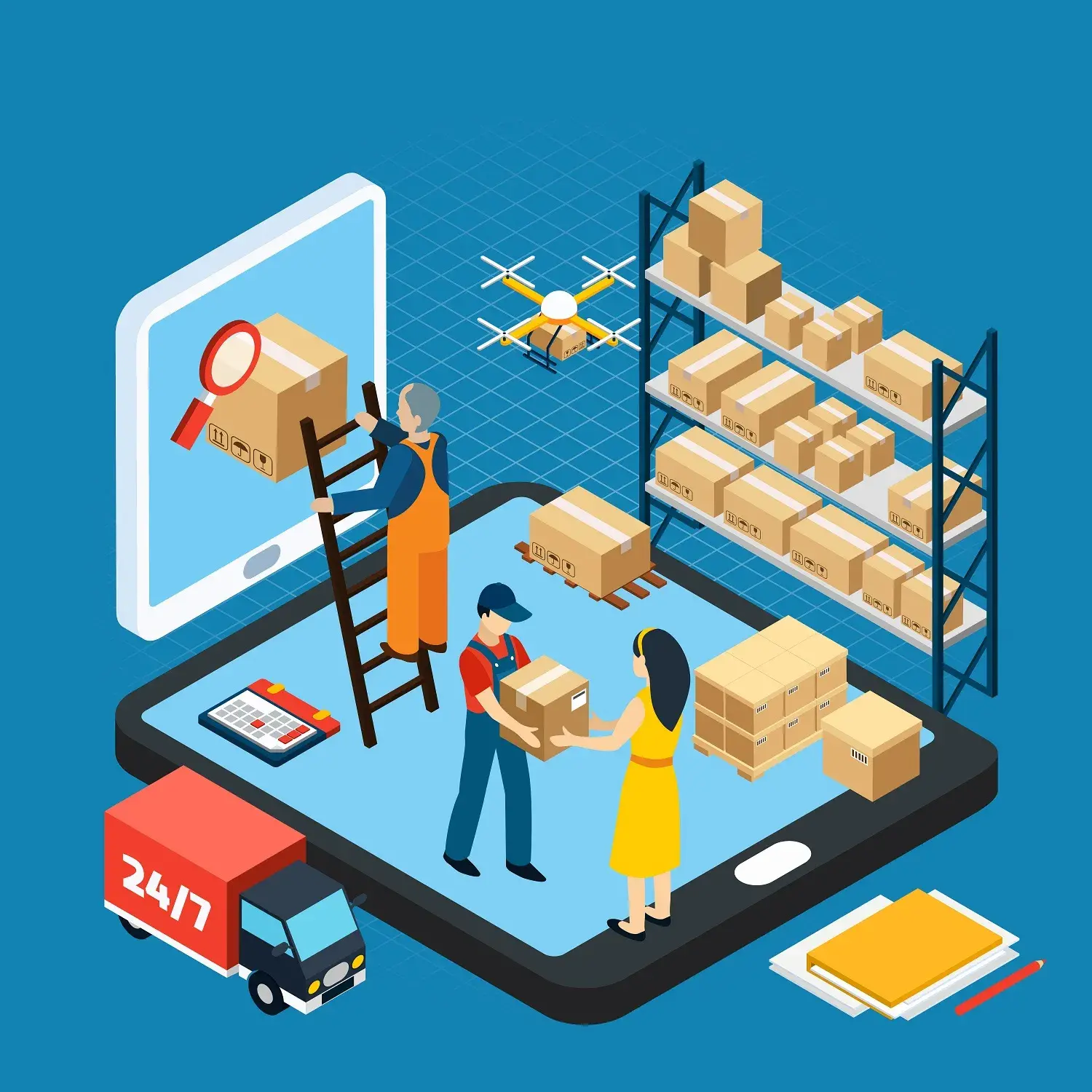
Lean Inventory Management: An Introduction to the Principles of Lean
Lean Inventory Management is an approach to inventory management that focuses on maximizing efficiency and minimizing waste in the inventory management process. It involves implementing strategies such as Just-in-Time (JIT) Inventory Management, Continuous Improvement, Kanban System, Total Quality Management (TQM), and Cross-Functional Collaboration to optimize inventory levels and reduce the costs associated with inventory holding […]
Read More
Kanban System in Inventory Management: An Introduction to Lean Principles
The Kanban system is a lean manufacturing methodology that originated in Japan and is used to manage and control the flow of materials and inventory in a production environment. Its purpose to optimize the inventory levels and minimize waste by producing or ordering only what is needed, when it is needed, and in the right […]
Read More