Editorial Note: We are an inventory management software provider. While some of our blog posts may highlight features of our own product, we strive to provide unbiased and informative content that benefits all readers.
Inventory put away is the process of storing incoming inventory in a warehouse or other storage facility.
It involves receiving and inspecting incoming goods, sorting and classifying them, and placing them in designated storage locations.
Inventory put away is an important part of the inventory management process, as it helps to ensure that inventory is stored efficiently and accessibly.
A well-designed inventory put away process can help businesses to:
- Improve inventory accuracy
- Reduce inventory picking times
- Free up warehouse space
- Improve warehouse safety
- Reduce costs
There are a number of different inventory put away methods that businesses can use, depending on their specific needs and requirements. Some common methods include:
- SKU-based put away: This method involves storing items based on their stock keeping unit (SKU) number. This can be a good option for businesses with a large variety of items, as it makes it easy to find and pick items.
- Zone-based put away: This method involves storing items in designated zones within the warehouse. This can be a good option for businesses with a smaller variety of items, or for businesses that need to store items together based on their characteristics (e.g., size, weight, etc.).
- Random put away: This method involves storing items in any available storage location. This can be a good option for businesses with a limited amount of storage space, or for businesses that need to be able to access items quickly.
The best inventory put away method for a business will depend on a number of factors, such as the size and type of inventory, the warehouse layout, and the business’s specific needs.
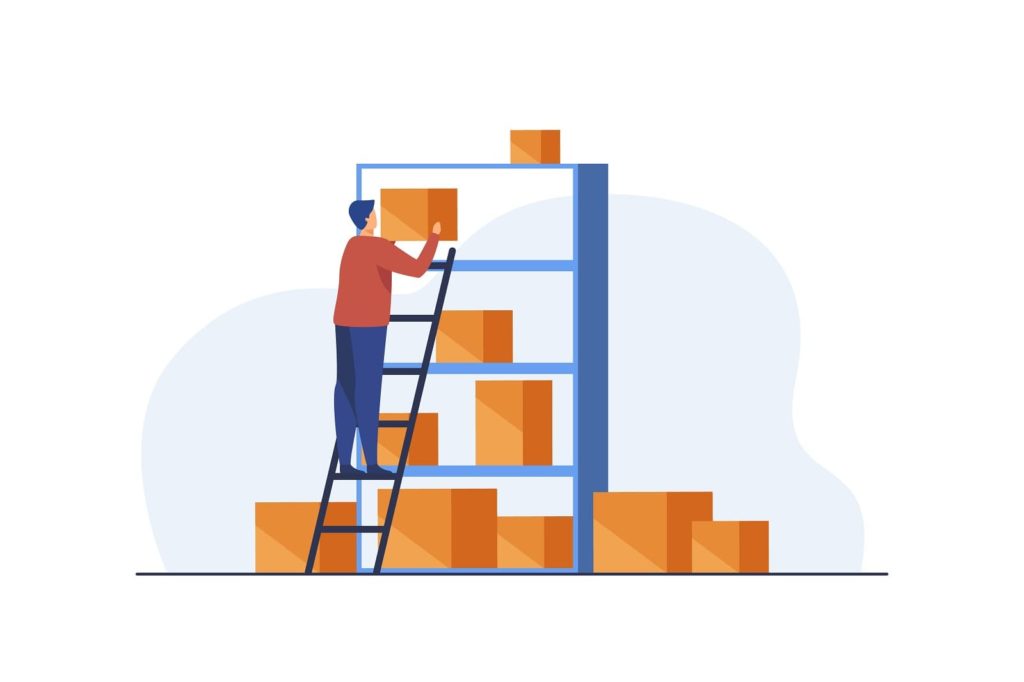
Here are some tips for efficient and accessible inventory put away:
- Plan your put away process carefully. Consider your inventory needs and goals, and determine the best layout for your storage space.
- Implement a put away system that is easy to follow and maintain. This will help to ensure that inventory is put away correctly and consistently.
- Use technology to automate tasks whenever possible. This can help to free up your staff to focus on other tasks, and it can also help to improve the accuracy of your put away process.
- Train your staff on the put away process. This will help to ensure that everyone is on the same page and that inventory is put away correctly.
- Monitor and measure your put away performance. This will help you to identify areas for improvement and to make sure that your put away process is meeting your needs.
Why Is It Important to Store Inventory Efficiently and Accessibly?
Storing inventory efficiently and accessibly is important for a number of reasons, including:
- Improved inventory accuracy: When inventory is stored in a well-organized and efficient manner, it is easier to track and manage. This can help to reduce inventory errors and ensure that businesses have accurate inventory records.
- Reduced inventory picking times: When inventory is stored in a way that is easy to access, warehouse workers can pick items more quickly and efficiently. This can help to improve order fulfillment times and reduce costs.
- Freed up warehouse space: Efficient inventory storage can help businesses to free up warehouse space. This can be used to store more inventory, or it can be used for other purposes, such as production or shipping.
- Improved warehouse safety: When inventory is stored in a safe and organized manner, it is less likely to be damaged or lost. This can help to improve warehouse safety and reduce costs.
- Reduced costs: Efficient inventory storage can help businesses to reduce costs in a number of ways, such as by reducing inventory errors, reducing inventory picking times, and freeing up warehouse space.
In addition to these benefits, efficient and accessible inventory storage can also help businesses to:
- Improve customer service by ensuring that products are available when customers need them.
- Reduce stockouts and backorders.
- Increase sales by being able to meet customer demand.
- Improve profitability by reducing costs and increasing sales.
Overall, storing inventory efficiently and accessibly is an important part of running a successful business. By taking the time to implement a well-designed inventory put away process, businesses can reap a number of benefits, including improved inventory accuracy, reduced inventory picking times, freed up warehouse space, improved warehouse safety, and reduced costs.
Planning Your Inventory Put Away Process:
Planning your inventory put away process is the first step to ensuring that it is efficient and effective. Here are some things to consider:
- Consider your inventory needs and goals. What types of inventory do you have? How much inventory do you have? What are your inventory turnover goals? What are your customer service goals? Once you have a good understanding of your inventory needs and goals, you can start to design a put away process that meets those needs.
- Determine the best layout for your storage space. Where is your inventory going to be stored? How much space do you have? How will you organize the space? You want to design a layout that is efficient and easy to navigate. You should also consider factors such as the weight and size of your inventory, as well as the frequency at which it is picked.
- Implement a put away system that is easy to follow and maintain. Your put away system should be clear, concise, and easy to follow for all employees. It should also be flexible enough to accommodate changes in your inventory or storage space.
Here are some specific tips for planning your inventory put away process:
- Use a warehouse management system (WMS). A WMS can help you to automate many of the tasks involved in inventory put away, such as generating put away labels and tracking inventory locations. This can help to improve the accuracy and efficiency of your put away process.
- Create a put away map. A put away map is a visual representation of your storage space, showing where different items should be stored. This can help employees to quickly and easily find the right location to put away inventory.
- Develop put away procedures. Put away procedures should describe the steps that employees need to follow when putting away inventory. This can help to ensure that inventory is put away consistently and correctly.
- Train employees on the put away process. All employees who are involved in inventory put away should be trained on the procedures that they need to follow. This will help to reduce errors and improve the efficiency of the process.
By carefully planning your inventory put away process, you can set yourself up for success. A well-designed put away process can help you to improve inventory accuracy, reduce picking times, free up warehouse space, improve safety, and reduce costs.
Executing Your Inventory Put Away Process:
Once you have planned your inventory put away process, it is time to execute it. Here are the basic steps involved:
- Receive and inspect incoming inventory. When inventory arrives, it should be received and inspected to ensure that it is accurate and in good condition. Any discrepancies should be documented and reported immediately.
- Sort and classify inventory. Once inventory has been received and inspected, it needs to be sorted and classified. This involves grouping items together based on their size, weight, type, or other criteria. This will make it easier to put away the inventory and to find it when it is needed.
- Place inventory in designated storage locations. Once inventory has been sorted and classified, it needs to be placed in designated storage locations. This should be done according to your put away map and procedures.
- Update inventory records. Once inventory has been put away, the inventory records need to be updated to reflect the new locations of the items. This will help to ensure that inventory is tracked accurately.
Here are some tips for executing your inventory put away process efficiently and effectively:
- Use a WMS. A WMS can help you to automate many of the tasks involved in inventory put away, such as generating put away labels and tracking inventory locations. This can help to improve the accuracy and efficiency of your put away process.
- Use barcode scanners. Barcode scanners can help to improve the accuracy and speed of inventory put away.
- Train employees on the put away process. All employees who are involved in inventory put away should be trained on the procedures that they need to follow. This will help to reduce errors and improve the efficiency of the process.
- Monitor and measure your put away performance. Track metrics such as put away time and accuracy to identify areas for improvement.
By following these tips, you can execute your inventory put away process efficiently and effectively. This will help you to improve inventory accuracy, reduce picking times, free up warehouse space, improve safety, and reduce costs.
Here are some additional tips:
- Use batch put away. Batch put away is a method of putting away inventory in groups. This can be more efficient than putting away individual items, especially if you have a large volume of inventory to put away.
- Use cross-docking. Cross-docking is a method of moving inventory directly from the receiving dock to the shipping dock, without putting it away in storage. This can be a good option for businesses that have a high turnover of inventory.
- Use put away zones. Put away zones are designated areas in the warehouse where specific types of inventory are stored. This can make it easier and faster to put away inventory.
By following these tips, you can optimize your inventory put away process and improve the efficiency and accuracy of your warehouse operations.
Optimizing Your Inventory Put Away Process:
There are a number of ways to optimize your inventory put away process. Here are a few tips:
- Use technology. A warehouse management system (WMS) can help you to automate many of the tasks involved in inventory put away, such as generating put away labels and tracking inventory locations. This can help to improve the accuracy and efficiency of your put away process. You can also use barcode scanners to improve the speed and accuracy of data entry.
- Optimize your warehouse layout. Consider the size and weight of your inventory, as well as the frequency at which it is picked, when designing your warehouse layout. You want to create a layout that is efficient and easy to navigate. For example, you may want to store high-volume items in easily accessible locations.
- Implement a put away system. Your put away system should be clear, concise, and easy to follow for all employees. It should also be flexible enough to accommodate changes in your inventory or storage space.
- Train employees. All employees who are involved in inventory put away should be trained on the procedures that they need to follow. This will help to reduce errors and improve the efficiency of the process.
- Monitor and measure your performance. Track metrics such as put away time and accuracy to identify areas for improvement.
Here are some additional tips for optimizing your inventory put away process:
- Use batch put away. Batch put away is a method of putting away inventory in groups. This can be more efficient than putting away individual items, especially if you have a large volume of inventory to put away.
- Use cross-docking. Cross-docking is a method of moving inventory directly from the receiving dock to the shipping dock, without putting it away in storage. This can be a good option for businesses that have a high turnover of inventory.
- Use put away zones. Put away zones are designated areas in the warehouse where specific types of inventory are stored. This can make it easier and faster to put away inventory.
- Use slotting optimization. Slotting optimization is a process of determining the best location to store each item in your inventory. This can help to improve put away and picking times, as well as reduce travel distances.
- Use put away rules. Put away rules can be used to automate the put away process and ensure that inventory is put away in the correct location. For example, you could create a rule that says that all high-value items must be stored in a secure area.
By following these tips, you can optimize your inventory put away process and improve the efficiency and accuracy of your warehouse operations.
Common Inventory Put Away Mistakes to Avoid:
Here are some common inventory put away mistakes to avoid:
- Not verifying inventory before putting it away. It is important to verify the quantity and condition of inventory before putting it away. This will help to identify any errors or discrepancies.
- Putting away inventory in the wrong location. Inventory should be put away in designated storage locations according to your put away system. This will help to ensure that inventory can be easily found and picked when it is needed.
- Not updating inventory records after putting away inventory. Inventory records should be updated after inventory has been put away to reflect the new locations of the items. This will help to ensure that inventory is tracked accurately.
- Not training employees on the put away process. All employees who are involved in inventory put away should be trained on the procedures that they need to follow. This will help to reduce errors and improve the efficiency of the process.
- Not monitoring and measuring put away performance. It is important to track metrics such as put away time and accuracy to identify areas for improvement.
Here are some additional tips to avoid common inventory put away mistakes:
- Use clear and concise put away labels. Put away labels should clearly indicate the item number, quantity, and storage location.
- Use barcode scanners to scan put away labels. This will help to improve the accuracy of data entry.
- Implement a put away system that is easy to follow. The put away system should be clearly documented and communicated to all employees.
- Train employees on the put away system. All employees should be trained on the procedures that they need to follow when putting away inventory.
- Regularly audit inventory. This will help to identify any discrepancies in inventory records.
By avoiding these common mistakes, you can improve the accuracy and efficiency of your inventory put away process.
Best Practices for Inventory Storage:
Here are some best practices for inventory storage:
- Organize your inventory logically. This will make it easier to find and pick items when you need them. You can organize inventory by type, size, weight, or popularity.
- Store inventory in a safe and secure location. This will help to protect your inventory from theft, damage, and environmental hazards.
- Label all inventory clearly. This will help to identify items quickly and easily. You can use barcode labels or human-readable labels.
- Use appropriate storage equipment. This may include shelving, racks, bins, or pallets. Choose storage equipment that is the right size and weight capacity for your inventory.
- Rotate inventory regularly. This will help to ensure that older items are used before they expire or become obsolete.
- Track inventory levels. This will help you to avoid stockouts and overstocking. You can use a manual or automated inventory tracking system.
Here are some additional tips for best practices in inventory storage:
- Store high-value items in a secure area. This could be a locked room or cabinet.
- Store hazardous materials in a designated area. This area should be well-ventilated and away from other inventory.
- Store flammable materials in a fireproof cabinet.
- Store food items in a cool, dry place.
- Store temperature-sensitive items in a temperature-controlled environment.
- Protect inventory from pests by regularly inspecting for and treating infestations.
- Keep storage areas clean and tidy. This will help to prevent accidents and make it easier to find items.
By following these best practices, you can ensure that your inventory is stored safely and efficiently. This will help you to reduce costs and improve customer service.
Conclusion:
Inventory put away is an important part of the inventory management process. By planning, executing, and optimizing your inventory put away process, you can improve inventory accuracy, reduce picking times, free up warehouse space, improve safety, and reduce costs.
Here are some key takeaways:
- Plan your inventory put away process carefully. Consider your inventory needs and goals, and determine the best layout for your storage space. Implement a put away system that is easy to follow and maintain.
- Execute your inventory put away process efficiently and effectively. Receive and inspect incoming inventory, sort and classify inventory, place inventory in designated storage locations, and update inventory records.
- Optimize your inventory put away process by using technology, training employees, and monitoring and measuring your performance.
By following these tips, you can improve your inventory put away process and improve the efficiency and accuracy of your warehouse operations.
Take a Quiz Test - Test Your Skill
Test your inventory management knowledge. Short multiple-choice tests, you may evaluate your comprehension of Inventory Management.