Editorial Note: We are an inventory management software provider. While some of our blog posts may highlight features of our own product, we strive to provide unbiased and informative content that benefits all readers.
Inventory accounting plays a crucial role in accurately valuing and managing a company’s inventory assets. It involves assigning costs to inventory and properly documenting it in financial records.
This comprehensive guide will provide you with a deep understanding of inventory accounting, its methods, and its impact on profit and taxation.
We’ll explore the different types of inventory, the importance of accurate valuation, and the various inventory accounting methods available.
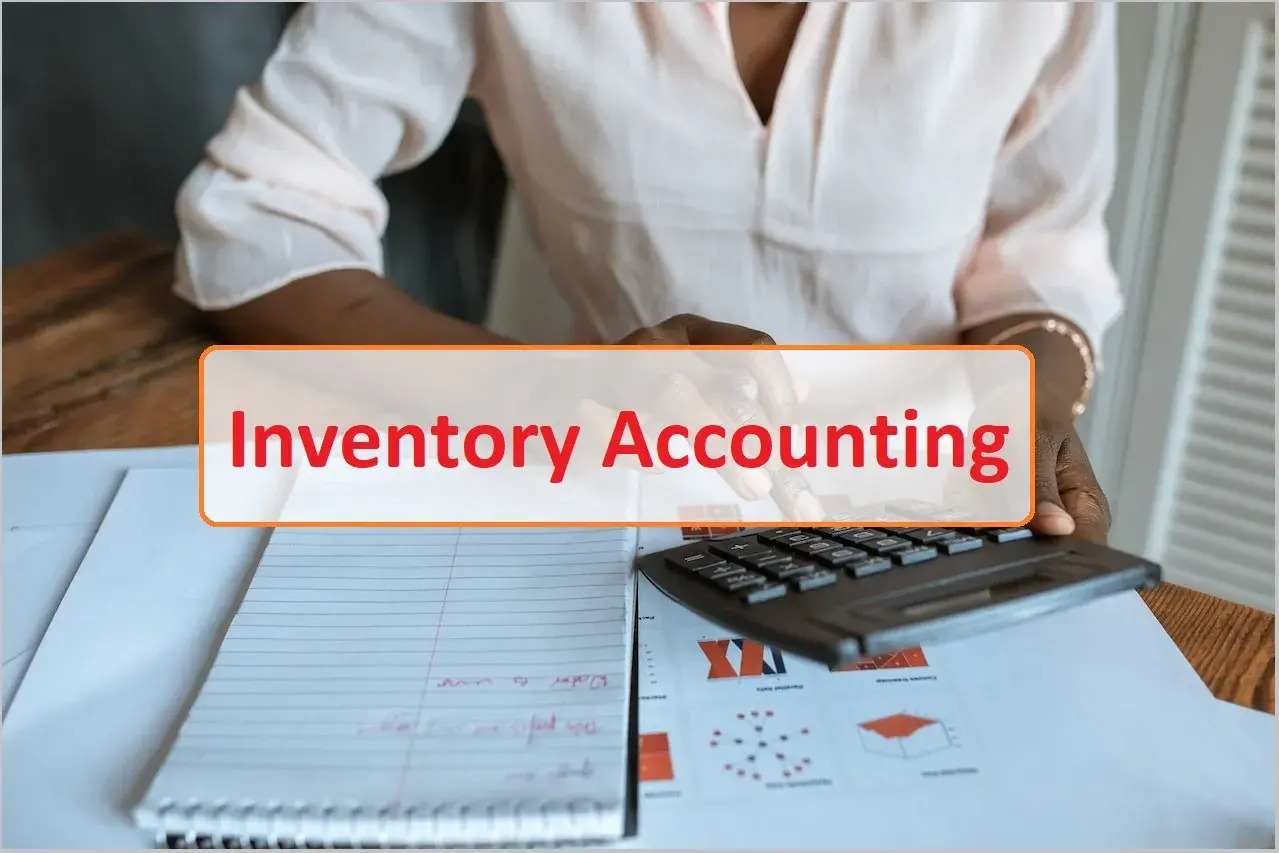
Introduction to Inventory Accounting
Inventory accounting is the process of accurately valuing and recording a company’s inventory assets. It is essential for maintaining proper financial records and complying with accounting standards. Inventory includes raw materials, work in progress, and finished goods held by a company. Assigning a value to inventory is crucial as it impacts the cost of goods sold and ultimately the company’s profitability. In this guide, we will delve into the intricacies of inventory accounting and explore the various methods used to value inventory.
Understanding Inventory Assets
Inventory assets refer to the goods and materials that a business holds for production, sale, or distribution. There are different types of inventory, including raw materials, work in progress, and finished goods. Raw materials are the basic components used in production, while work in progress represents products that are still being manufactured. Finished goods are the final products ready for sale to customers.
1. Types of Inventory
Inventory can take different forms depending on the nature of the business. It can include raw materials, which are the basic components used in production. Work in progress refers to partially completed products that are still undergoing manufacturing processes. Finished goods are the final products ready for sale to customers. Properly categorizing inventory is essential for accurate valuation and tracking.
2. Valuing Inventory
Accurately valuing inventory is crucial for financial reporting and decision-making. It involves determining the cost of inventory, including direct costs such as materials and labor, as well as indirect costs like overhead expenses. The value of inventory can fluctuate based on market conditions, obsolescence, and other factors. Regular inventory audits and tracking systems are necessary to maintain accurate valuation.
The Basics of Inventory Accounting
Inventory accounting involves calculating the cost of goods sold (COGS) and determining the value of ending inventory using different cost flow assumptions, such as FIFO or LIFO, to ensure accurate financial reporting and informed decision-making.
1. The Cost of Goods Sold
The cost of goods sold (COGS) is a key component of a company’s financial statements. It represents the direct costs incurred in producing or acquiring the goods sold during a specific period. Calculating COGS involves considering the beginning inventory, purchases or production costs, and ending inventory. Accurately determining the value of ending inventory is crucial for calculating the COGS and ultimately determining the company’s profitability.
2. Determining the Value of Ending Inventory
The value of ending inventory is determined by the cost flow assumption chosen by the company. Common methods include first in, first out (FIFO), last in, first out (LIFO), weighted average, and specific identification. Each method has its advantages and considerations, such as the impact on profitability, tax obligations, and inventory turnover. Choosing the right method is crucial for accurate financial reporting and decision-making.
Common Inventory Accounting Methods
Inventory accounting methods such as FIFO and LIFO offer different approaches to valuing inventory and determining the cost of goods sold, with implications for profitability and tax obligations. The weighted average method provides a blended cost, while the specific identification method tracks individual costs, each offering their own advantages and considerations.
1. First In, First Out (FIFO)
The FIFO method assumes that the first items purchased or manufactured are the first ones sold or used. This method aligns with the natural flow of inventory in many companies and is commonly used in industries where product expiration is a concern. FIFO can result in higher profitability and tax obligations as older, lower-cost inventory is assigned to COGS first.
2. Last In, First Out (LIFO)
The LIFO method assumes that the last items purchased or manufactured are the first ones sold or used. This method may not align with the actual flow of inventory in many companies but can be advantageous for tax purposes. LIFO can result in lower profitability and tax obligations as the cost of the most recent, higher-priced inventory is assigned to COGS first.
3. Weighted Average Method
The weighted average method calculates the average cost of all items in inventory and assigns this average cost to each unit sold. This method is useful when individual identification of inventory items is not practical or necessary. It provides a blended cost that can be helpful for cost control and pricing decisions.
4. Specific Identification Method
The specific identification method involves tracking the cost of each inventory item separately and assigning the specific cost to each unit sold. This method is typically used for high-cost items or unique products. It provides precise cost information for each unit sold but requires extensive record-keeping and may not be practical for all businesses.
Choosing the Right Inventory Accounting Method
When choosing an inventory accounting method, retailers should consider factors like seasonality and perishability, while manufacturers should align with production cycles, and wholesalers may opt for FIFO or weighted average methods based on their requirements.
1. Considerations for Retailers
Retailers often deal with large volumes of inventory and must choose an accounting method that aligns with their inventory turnover and sales patterns. Factors to consider include seasonality, perishability, and pricing strategies. FIFO may be suitable for retailers with perishable goods, while LIFO may be advantageous for retailers facing rising prices.
2. Considerations for Manufacturers
Manufacturers must consider the flow of inventory from raw materials to finished goods and choose an accounting method that accurately reflects this flow. FIFO may be suitable for manufacturers with consistent production processes, while LIFO may be beneficial for those facing rising material costs. The choice of method should align with the company’s production cycle and inventory management practices.
3. Considerations for Wholesalers
Wholesalers often deal with a wide range of inventory items and must choose an accounting method that accommodates varying costs and turnover rates. The choice of method should consider factors such as product obsolescence, market fluctuations, and pricing strategies. Wholesalers may opt for FIFO or weighted average methods depending on their specific requirements.
Implications of Inventory Accounting
The choice of inventory accounting method can have significant implications for a company’s profitability, affecting figures such as cost of goods sold, gross margins, and net income.
1. Profit and Loss Impact
The choice of inventory accounting method can directly impact a company’s profitability. Different methods can result in varying cost of goods sold figures, gross margins, and net income. Businesses must carefully assess the potential impact on profitability when selecting an inventory accounting method.
2. Taxation Impact
Inventory accounting methods can also affect a company’s tax obligations. Methods like LIFO can result in lower taxable income due to higher COGS figures, potentially reducing the tax burden. However, tax regulations and reporting requirements vary by jurisdiction, and businesses should consult with tax professionals to ensure compliance.
Best Practices for Effective Inventory Management
Effective inventory management practices include implementing inventory control systems for accurate tracking and automation, conducting regular audits to maintain accurate records, and utilizing demand forecasting and strong supplier relationships to optimize inventory levels and minimize supply chain disruptions.
1. Implementing Inventory Control Systems
To ensure accurate inventory accounting, businesses should implement robust inventory control systems. These systems can track inventory levels, monitor stock movements, and facilitate real-time data analysis. Automated systems can streamline inventory management processes and reduce manual errors.
2. Regular Inventory Audits
Regular inventory audits are essential for maintaining accurate inventory records. Audits help identify discrepancies between recorded inventory and physical counts, detect theft or loss, and ensure compliance with accounting standards. Businesses should establish audit procedures and schedules to maintain the integrity of their inventory data.
3. Forecasting and Demand Planning
Accurate demand forecasting is crucial for managing inventory levels effectively. By analyzing historical sales data, market trends, and customer preferences, businesses can optimize inventory levels and avoid stockouts or excess inventory. Demand planning tools and techniques can help businesses make informed decisions about purchasing, production, and inventory replenishment.
4. Supplier Relationship Management
Building strong relationships with suppliers is essential for efficient inventory management. Collaborating with suppliers can lead to better pricing, timely deliveries, and improved inventory availability. Clear communication, data sharing, and mutually beneficial agreements can help businesses maintain optimal inventory levels and minimize supply chain disruptions.
The Role of Technology in Inventory Accounting
Technology, such as inventory management software and automated tracking systems, plays a pivotal role in inventory accounting by streamlining processes, improving accuracy, and providing real-time visibility, while integration with accounting systems eliminates manual data entry and enhances decision-making capabilities.
1. Inventory Management Software
Inventory management software provides businesses with tools to streamline inventory accounting processes. These systems can automate inventory tracking, generate real-time reports, and integrate with accounting systems for seamless financial record-keeping. Advanced features such as barcode scanning, SKU tracking, and demand forecasting enhance accuracy and efficiency in inventory management.
2. Automated Tracking Systems
Automated tracking systems, such as RFID (Radio Frequency Identification) or barcode systems, enable real-time monitoring of inventory movements. These systems can improve accuracy, reduce manual errors, and enhance inventory visibility. By automating data capture and updating, businesses can maintain accurate inventory records and streamline inventory accounting processes.
3. Integration with Accounting Systems
Integrating inventory management systems with accounting software ensures seamless flow of data between inventory and financial records. This integration eliminates the need for manual data entry, reduces errors, and provides real-time visibility into inventory costs, sales, and profitability. By centralizing data, businesses can make informed decisions and streamline their inventory accounting processes.
Case Studies: Successful Inventory Accounting Strategies
Successful inventory accounting strategies include implementing FIFO for perishable goods, reducing waste, and improving profit margins, as well as utilizing LIFO to optimize inventory turnover, manage costs, and make informed pricing decisions. The weighted average method can be leveraged to accommodate fluctuating market prices, maintain cost efficiency, and accurately track inventory valuation.
Company A: Implementing FIFO for Improved Profit Margins
Company A, a retailer in the food industry, implemented the FIFO inventory accounting method to better manage perishable goods. By ensuring older inventory was sold first, they reduced waste and improved profit margins. The FIFO method allowed them to accurately track inventory costs, optimize pricing strategies, and maintain compliance with accounting standards.
Company B: Optimizing Inventory Turnover with LIFO
Company B, a manufacturer facing rising material costs, implemented the LIFO inventory accounting method to optimize inventory turnover. By assigning higher costs to COGS, they reduced taxable income and improved cash flow. The LIFO method enabled them to manage inventory costs effectively and make informed pricing decisions.
Company C: Leveraging the Weighted Average Method for Cost Efficiency
Company C, a wholesaler dealing with fluctuating market prices, adopted the weighted average method for inventory accounting. This method allowed them to assign a blended cost to each unit sold, accommodating varying purchase prices. By leveraging the weighted average method, they maintained cost efficiency, managed inventory turnover, and accurately tracked inventory valuation.
Conclusion
Inventory accounting is a critical aspect of managing a company’s inventory assets. Accurate valuation and proper accounting methods are essential for financial reporting, profit analysis, and taxation purposes.
By understanding the different inventory accounting methods and implementing best practices in inventory management, businesses can optimize profitability, streamline operations, and make informed decisions. Embracing technology and leveraging automated systems can further enhance accuracy and efficiency in inventory accounting.
With careful consideration and implementation of inventory accounting strategies, businesses can effectively manage their inventory assets and drive success in today’s competitive market.
Take a Quiz Test - Test Your Skill
Test your inventory management knowledge. Short multiple-choice tests, you may evaluate your comprehension of Inventory Management.